Projectile tube cleaning
For heat exchanger- and condenser tubes
Dart cleaning is a low-pressure, high-speed method for cleaning large numbers of (surface) condenser- and heat exchanger tubes. Special projectiles are shot through the tubes with low-pressure pump systems. A projectile tube cleaning is currently the fastest technology available: 2 operators are able to clean roughly 500 tubes/hour. This figure is easily scalable by increasing the operator count.
Abalco is an (industrial) cleaning company located in The Netherlands. From our central location in Werkendam, we offer complete tube cleaning services but can also provide on-site support and assist with project start-ups together with local contractors or staff. Abalco has developed unique and state-of-the-art propulsion equipment, designed to clean a large number of tubes in a safe, cost-effective, fast, and environmentally friendly way.

Projectiles (darts) are selected based on the tube inner diameter, expected deposits, and other factors. Darts are shot through the tubes at low pressure and remove all types of fouling, often mud, bio-fouling, barnacles, and scaling. The entire cleaning process takes less than 5 seconds/tube, regardless of the length.
APPLICATIONS
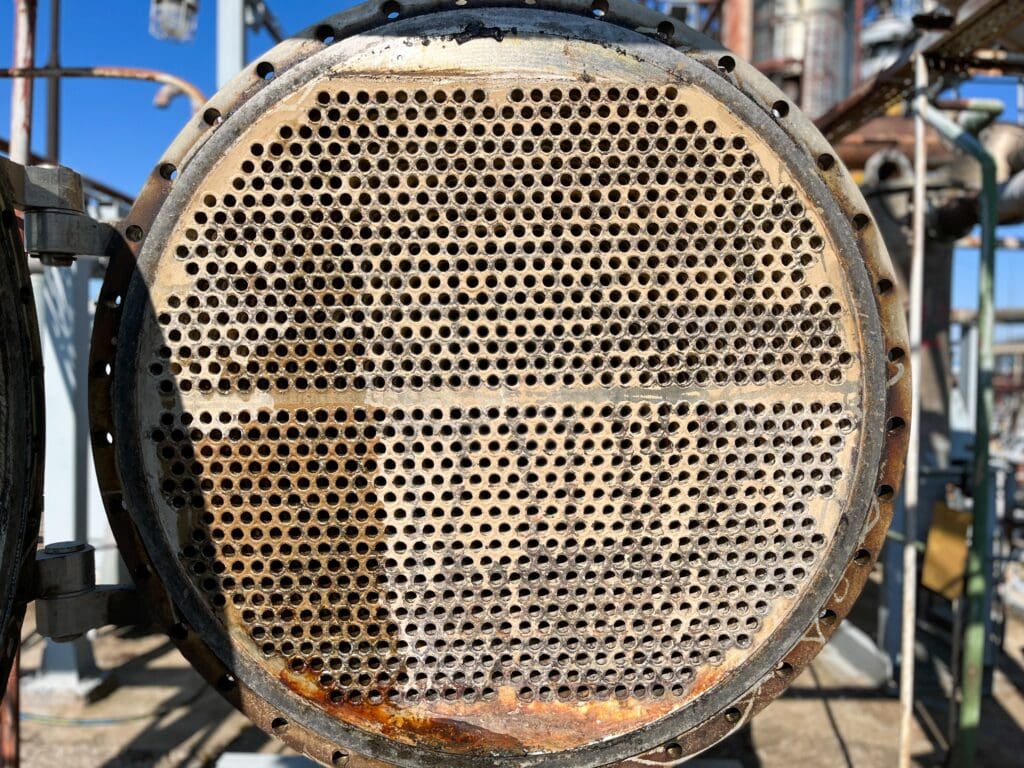
SHELL & TUBE HEAT EXCHANGERS
Straight, smooth heat exchanger tubes can be cleaned with projectiles. Dart cleaning reduces cleaning downtime and offers safe and effective cleaning.
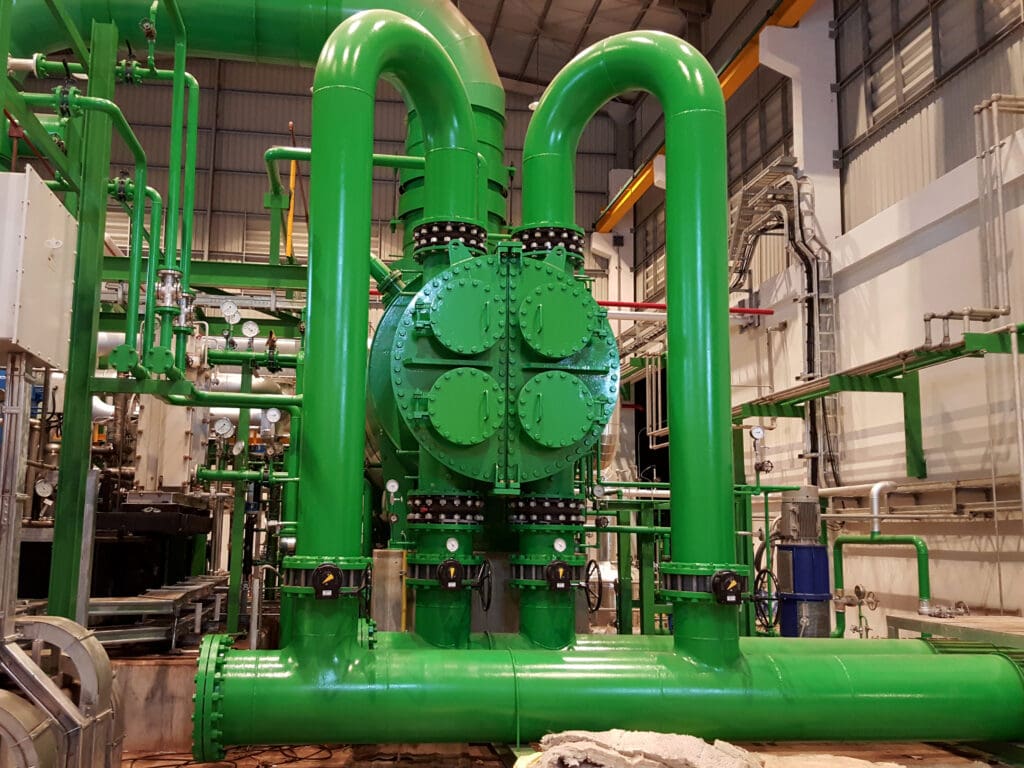
STEAM SUFRFACE CONDENSERS
Condensers play a crucial role in power generation plants. Clean tubes are vital for the efficiency of the plant. Dart cleaning significantly reduces the downtime due to cleaning.
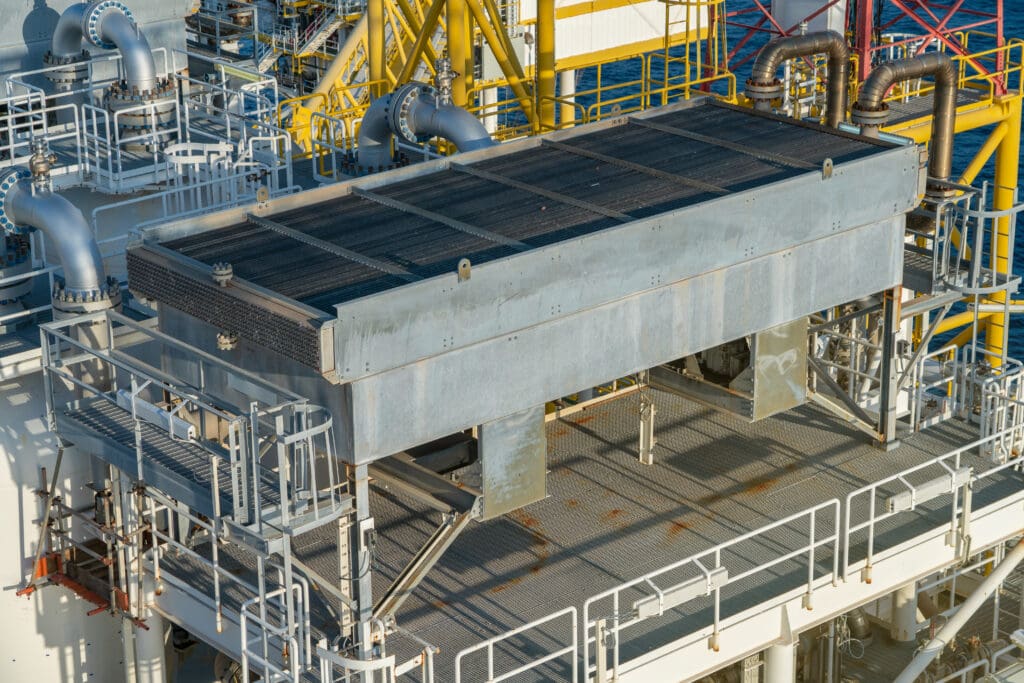
AIRFIN PROCESS COOLERS (TUBE SIDE)
Airfin coolers generally have long tubes. By shooting through projectiles, a large number of tubes can be cleaned with minimal manpower and great results.
OUR EQUIPMENT
HOW DOES IT WORK?
A step-by-step explanation of dart cleaning
Heat exchanger or condenser tubes will become fouled over time. Often times, deposits like algae, mud, slime, silt, barnacles, mussels, biofouling, and (light) scaling will adhere to the tube walls. By doing so, they create an isolating barrier which negatively impacts the heat transfer coefficient. In other words, the system’s performance will decrease due to deposits inside the tubes. Even heat exchangers with automatic (online) ball cleaning systems will become fouled over time. An offline cleaning will be necessary to get the tubes clean again.
After deciding to perform an offline cleaning to restore efficiency levels, it is possible to choose from different cleaning technologies. Dart cleaning is a safe, fast, and cost-effective technology to clean heat exchanger and condenser tubes. When cleaning with projectiles, it is important to have all the necessary data at hand, such as the expected deposits, tube material, inner diameter, and length. It’s also good to know what kind of cleaning (if any) has taken place in the past.
When all data has been collected, it is time to choose the right type of projectile which will be used to shoot through the tubes and remove the deposits. The experts of Abalco’s DCS team are able to assist with recommendations based on your information and our experience. Projectiles are reusable and travel through the tubes at high speed. Often times, they remove all deposits inside the tube within a single pass.
Projectiles are loaded into the tubes and shot through with specialized equipment, also known as propulsion systems. These systems use a high waterflow of ca. 130 liters/minute to push the projectiles through the tubes. The high waterflow also causes turbulence inside the tubes, which increases the cleaning effect and also flushes out loosened deposits. The entire cleaning process is performed with a low pressure of only 40 bar, which greatly contributes to the safety of the operators and equipment.
A special catching net is attached to the other side of the heat exchanger or condenser. This net is used to catch the projectiles when they exit the tubes. By catching the projectiles safely, maximum reusability is ensured. After projectiles are caught and cleaned, they can be reused. The amount of times a projectile can be used, depends on the type, tube length, deposits, etc. More information can be found on the ”projectiles” page.
After cleaning, it is important to inspect all tubes for potential blockages or stuck projectiles. By performing a light test, a large number of tubes can be inspected in a short period of time. Often times a blockage is just a tube that had been missed during cleaning. By flushing it, the blockage or stuck projectile is often removed right away. In case this doesn’t work, the deposit/projectile can be pushed out with a fiberglass rod.
When the cleaning and inspection has been completed, the heat exchanger or condenser can be returned to service. With the tubes now being clean, it is wise to consider implementing a preventive mechanical tube cleaning strategy. For example, every 1 or 2 years the heat exchanger or condenser is cleaned with projectiles, ensuring maximum efficiency and less hard deposit buildup over time. Furthermore, by doing this, potential tube leaks caused by under deposits- or microbiologically induced corrosion is prevented as much as possible.
ABOUT ABALCO
The Abalco Group specializes in the cleaning of various heating- and cooling systems. Throughout their various divisions, they serve all types of customers within Europe. Abalco’s dart cleaning technology is specifically interesting for power generation plants, refineries, and other large scale manufacturing plants that have shell and tube heat exchangers or steam surface condensers. Abalco has the option to provide a complete cleaning service, or work with local operators on-site by providing project managers for the project duration.